Discover More
New Tech
Traditional Tech
Emerging Tech
Multi-Tech
Companies
Products
Gas
Oil
Liquids
Regions
Measurement
Geometry
Philosophy
Jeans
Follow Us
FlowTime Clock ...
What
flowtime is it?
Time displayed is Flowtime.
|
Turbine flowmeters
have been around for many years.In fact, the generally accepted view places the
invention of the first turbine meter in 1790. However, it wasn’t until World
War II and afterwards that turbine meters began being used in industrial
environments. And even though turbine meters are facing competition today from
new-technology flowmeters, the turbine market is still very large, and is
growing in some segments.
The word “turbine” is derived from a Latin word
that means “spinning thing.” The ancient Greeks ground their flour using
horizontal turbine wheels. However, the idea of using a spinning rotor or
turbine to measure flow did not come about until much later in history. What
turbine meters have in common is the use of a rotor that spins in proportion to
flowrate.
For more information
on our new turbine flowmeter study, publishing in September 2022, go to www.flowturbine.com.
Click to learn
more about
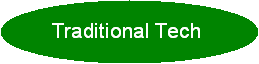
History and types
Reinhard Woltman is generally credited with the invention of the first turbine
flowmeter in 1790. Woltman was a German engineer who studied the loss of energy
in open canals. He published several works on hydraulic engineering in the
1790s. Today’s bulk meters, used to measure water flow in larger quantities,
are still called Woltman flowmeters. There are at least eight distinct types of
turbine flowmeters. Some turbine meters get their name and inspiration from
types of water wheels. Others are mainly used to measure the flow of water for
billing purposes. The types of turbine meters are as follows:
* Pelton wheel
* Paddlewheel
* Propeller
* Woltman
* Single jet
* Multi-jet
* Compound
* Axial
Pelton wheel. The origins of the Pelton wheel flowmeter go back to a type
of water wheel called the Pelton wheel. Lester Pelton (1831 – 1908) built the
first Pelton wheel water wheel in Camptonville, Nevada. A Pelton wheel turns as
a result of water jets that impinge on buckets attached around the outside of
the wheel. The wheel is connected to a turbine. The turning of the wheel rotates
the turbine and generates power. Lester Pelton formed the Pelton Water Wheel
Company in 1898. Today Pelton wheel flowmeters are used to measure low viscosity
flows at low flowrates.
Paddlewheel. Paddlewheel flowmeters are also based on the design of a
water wheel. Paddlewheel meters have a shaft at right angles to the flowstream.
They have a lightweight paddlewheel that spins in proportion to flowrate, and
are used to measure low-speed flows. Paddlewheel flowmeters are available in
both insertion and inline types.
Propeller. The origins of the propeller meter go back to the invention of
the propeller turbine, which is used for hydropower. Forrest Nagler designed the
first fixed-blade propeller turbine, which was installed in 1916. The propeller
turbine has from three to six blades, and resembles the propeller on a boat.
Because propeller turbines have fewer blades than some other turbines, they are
less likely to be damaged by debris in the water.
Today’s propeller meters are based on a similar principle. Propeller meters
face into the flow and have a single bearing assembly. While some people do not
consider propeller meters to be a type of turbine meter, they have a rotating
element whose rotation is proportional to flowrate. Propeller meters are
relatively low cost, and do not require power.
Woltman. Woltman meters have a turbine whose axis is in line with the
direction of flow. These meters are used in the municipal and industrial water
industry to measure larger flows. They are sometimes called “bulk” meters.
Their name goes back to Reinhard Woltman, who invented the first turbine
flowmeter in 1790.
Single jet. Single jet meters are widely used in residential and
commercial applications to measure the flow of water for billing purposes. In
single jet meters, water passes through an orifice, creating a stream or
“jet” of water. This jet of water is directed onto the impeller blades,
causing them to rotate.
Multi-jet. Like single jet meters, multi-jet meters are used in
residential and commercial applications to measure the flow of water for billing
purposes. Some are also used in industrial applications. Multi-jet meters have
several orifices creating several jets that are directed onto impeller blades,
causing them to rotate.
Compound. Compound meters are a type of hybrid meter that have a turbine
component. Compound meters are installed in apartment buildings and offices
where the flowrate varies between high and low flowrates. Flowrates might be
very high in apartment buildings in the morning and evening, for example, but be
very low or nonexistent at night. Compound meters typically have a turbine
component to handle high flowrates, and a positive displacement component to
handle the low flowates. They may also have a single jet or multi-jet turbine
for the lower flowrates.
Axial. Most of the turbine flowmeters used in industrial applications to
measure the flow of hydrocarbons, industrial liquids, and gases are called axial
turbine meters. Axial meters have a rotor that rotates around the axis of flow.
Axial meters differ according to the number and shape of the rotors. Axial
meters for liquids have a different design from axial meters for gases.
What turbine meters have in common is the use of a rotor that spins or rotates
in proportion to flowrate. Measuring flow in this way requires the capability of
detecting the rotational speed of the rotor. For this reason, the turbine meter
as it is used today had to await the invention of a pick-off sensor with a
magnet and a rotating conductor. This makes it possible to count the number of
rotations of a turbine rotor. In the early 1940s, turbine meters were developed
to accurately measure fuel consumption on military aircraft in World War II.
Soon after this time, turbine meters began to be used to measure the flow of
hydrocarbons.
The use of turbine meters to measure gas flow dates back to 1953. Rockwell
introduced an improved turbine meter to the gas industry in 1963. It took about
ten years for turbine meters to become accepted by the gas industry for
measuring gas flow. In 1981, the American Gas Association (AGA) published its
report #7, “Measurement of Fuel Gas by Turbine Meters.” Since that time,
turbine meters have been solidly established in the gas industry, especially for
custody transfer applications.
Where they are used
Turbine flowmeters are mainly used to measure the flow of fluids in the
following four segments:
* Municipal water
* Municipal and industrial gas
* Oil (hydrocarbons)
* Industrial liquids
Turbine meters used in the municipal water industry are widely used for billing
purposes. Some turbine meters are used for residential billing purposes,
especially single jet and multi-jet meters. However, nutating disc and
oscillating piston positive displacement meters dominate this market. Because
turbine meters excel at medium to high-speed flows, they are used more widely
for billing purposes in commercial and industrial markets. In this use, they are
sold to water and gas utility companies that install them in commercial and
industrial buildings to measure the amount of water and gas used in those
buildings.
Many manufacturing plants measure liquids and gases inside the plant as part of
the manufacturing process. These are considered to be industrial applications.
However, the water and gas that these plants use, when it is obtained from a
water or gas utility company, has to be measured for billing purposes. This is
considered to be a utility application, and is very similar to the measurement
of gas or water used by a hotel or office building.
Besides being used for utility gas measurement, turbine meters are also used to
for industrial gas measurement. The use of turbine meters to measure natural gas
for custody transfer purposes is an example of industrial gas measurement. A
number of companies sell into the turbine gas flow market, including Invensys,
Elster, Instromet, and Emerson Daniel.
Another important segment of the turbine flowmeter market is the market for
measuring hydrocarbon-based liquids. Both turbine and positive displacement
flowmeters are used to measure the flow in this segment. Turbine meters are used
to measure the transfer of hydrocarbons in trucking, aviation, petroleum
transportation, petroleum production, and petroleum terminals. These meters are
very different from the smaller jet-type meters, and are highly accurate and
rugged industrial meters. They are used because of their accuracy and their
reliability.
Turbine meters are also used to measure the flow of industrial liquids. This
measurement can occur within a manufacturing plant, or it may occur as a custody
transfer operation between plants. Chemical, food processing, refining, and
power plants are examples of some of the manufacturing plants that use turbine
flowmeters.
Turbine flowmeters still a viable
choice
Turbine meters belong to the class of traditional technology flowmeters. The
history of new-technology flowmeters begins after 1950, while the origins of
traditional technology meters predate 1950. Many traditional technology meters
have moving parts, and some are mechanical rather than electronic.
New-technology flowmeters include Coriolis, magnetic, ultrasonic, vortex, and
multivariable differential pressure (DP). Traditional technology flowmeters
include differential pressure, turbine, positive displacement, open channel, and
variable area.
There is a clearly identifiable trend today towards new-technology flowmeters
and away from traditional technology meters. However, despite this trend, there
are several reasons why traditional technology meters still extremely important
in today’s flowmeter market. One reason is that some of the traditional
technology flowmeter markets are so large that even if they are showing some a
slight decline, these meters still represent a very large volume of business
every year. For example, the worldwide turbine market exceeded $400 million in
2001.
Secondly, traditional technology meters still have a very large installed base.
This is certainly true of turbine meters. Turbine meters are very well
entrenched in gas flow measurement, in hydrocarbon liquid measurement, and in
the municipal water market. Because end-users often replace like with like, many
of them will continue to use turbine technology for many years to come.
Third, in some cases traditional technology flowmeters really are the best
solutions for certain types of flowmeter applications. For example, it is
difficult to find any flowmeter that handles low flowrates and high viscosity
fluids as well as positive displacement flowmeters. And turbine meters excel at
measuring the flow of clean medium to high-speed liquids and gases. They are
still widely used for this purpose.
Turbine meters also do not have some of the limitations that some new-technology
meters have. For example, turbine meters also do not have the same line size
constraint that limits the use of Coriolis meters to four inches and less, with
a few exceptions. They can also meter hydrocarbons, unlike magnetic flowmeters.
The main competitor to turbine flowmeters, especially in the larger sizes, is
ultrasonic flowmeters. This is especially true for natural gas flow, where
ultrasonic flowmeters received AGA approval in 1998 for use in custody transfer
of natural gas. DP flowmeters are also widely used in this context.
Turbine flowmeter manufacturers are also coming out with improvements that make
these meters more reliable and more competitive with new-technology meters. For
example, Hoffer Flow Controls has introduced turbine meters with hybrid ceramic
ball bearings, thereby increasing the reliability of their meters. Bopp &
Reuther is selling a HART-compatible turbine flowmeter. It is likely, in fact,
that more suppliers will incorporate features from new-technology flowmeters
into turbine meters in the future, such as advanced electronics, making them
both more reliable and better able to fit into today’s more advanced
instrument marketplace.
Another reason why traditional technology meters are holding their own or
growing in some segments is that industrial associations play a major role in
determining what meters are acceptable in some applications, especially for
billing purposes. And in some cases, traditional technology meters are all that
is specified. Until new-technology flowmeters receive approvals from the
standards bodies and industry associations, traditional technology meters will
continue to be used.
In the United States, for example, the American Water Works Association (AWWA)
is very influential in laying out criteria for water meters to conform to when
they are used for billing purposes. The AWWA has written reports approving both
turbine and positive displacement flowmeters for this purpose. The AWWA has
formed a committee to study issuing a report for magnetic flowmeters, but such a
report is still several years away. The organization is also looking at the
possibility of forming a committee for Coriolis meters, but has not yet done so.
In the meantime, single jet, multi-jet, Woltman, and positive displacement
meters dominate the municipal water industry.
Look for growth
There are many types of turbine flowmeters, and they are used for many different
applications. Even though the turbine market as a whole is showing a slow
decline or holding steady, some segments are experience growth, especially in areas where
new-technology flowmeters have not yet penetrated. There are still some
applications where turbine meters remain the best flow solution. Given their
very large installed based, and technological improvements being made by the
suppliers, turbine flowmeters will be around for many years to come.
|